Microstructural decay and fatigue nucleation from long term thermo-mechanical exposure
When high strength bearing steels are exposed to repeated rolling contact cycles at high loads the material below the contact eventually displays changes in the microstructure. The affected volume is small and comprises the highest stressed volume below the contact. The microstructural change of the material is often characterized by dark etching areas after 100 thousand to 100 million cycles followed by white bands after billions of cycles for maximum contact pressures above 3 GPa. It is of interest in the present project to develop a detailed understanding of the microstructural decay and to couple this with fatigue nucleation.
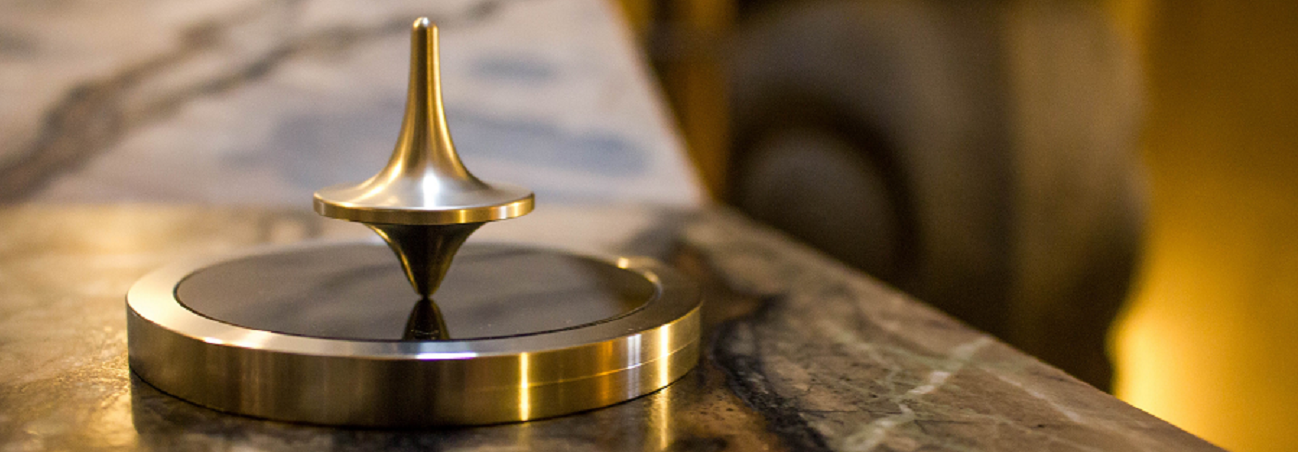
The purpose is to quantify microstructural decay of martensitic high strength steel from repeated long term thermomechanical exposure and the effects of the decay on fatigue nucleation and fatigue properties. Fatigue is the most common failure mode of many steel applications, in particular bearing applications where crack initiation constitutes over 90% of the component life. Many fatigue cracks and fatigue failures in high strength steels are initiated by defects such as non-metallic inclusions or surface irregularities. Excluding surface roughness and material inclusions, there still remains the increasingly important question of fatigue nucleation in the material microstructure and the fatigue preceding decay of the microstructure. Thus, the goal of the project is to develop a thorough scientific understanding of the microstructural decay of the material due to thermomechanical exposure and the underlying mechanisms of the succeeding fatigue nucleation. In particular, the project will focus on material decay and fatigue nucleation related to rolling contact fatigue in martensitic high strength bearing steels.
When high strength bearing steels are exposed to repeated rolling contact cycles at high loads the material below the contact eventually displays changes in the microstructure and in the raceway a shallow groove will form resulting in a somewhat larger and more conform contact. An investigation of the material cross-section just below the contact through an optical light microscope revealed that the material volume directly below the contact had changed colour to a slightly different grey tone, illustrating material change.
The affected volume is small and comprises the highest stressed volume below the contact. During each over-rolling cycle a volume below the contact surface is exposed to a stress cycle consisting of increasing compressive normal stress in combination with a substantial shear stress. As the compressive stress increases the shear stress reaches a maximum and then it decreases back to zero at the compressive maximum, which coincides with the instance when the bearing roller is straight above the considered material volume. As the over-rolling sequence continues the normal stress is unloaded and a symmetric shear cycle is inflicted in the opposite direction to that during loading.
The microstructural change of the stressed material volume below a rolling contact is often characterized by dark etching areas after 105 to 108 cycles followed by white bands after 108 to 1010 cycles for maximum contact pressures above 3 GPa. It is of interest in the present project to develop a detailed understanding of the microstructural decay and to couple this with fatigue nucleation.
The personel involved in the project are as follows:
- Ph.D.-student at the Department of Materials Science and Engineering, KTH: Tania Loaiza Uribe.
- Industrial supervisors and participants at Ovako: Steve Ooi, Patrik Ölund, Fredrik Lindberg and Jan-Erik Andersson,
- Ph.D. supervisors at the Department of Materials Science and Engineering, KTH: Peter Hedström (main supervisor), Prasath Babu Revathy Rajan and Annika Borgenstam.
- Ph.D. supervisor at the Unit of Solid Mechanics, KTH: Bo Alfredsson.