Development of a tool to predict mechanical properties of powder based metals containing porosity
Materials manufactured from powder based technologies, such as compaction and sintering or additive manufacturing, are characterized both by the unique microstructures that can be obtained from different alloying techniques as well as the porosity that is often present in the materials. Thus the models used to analyze these materials must be able to take these factors into account.
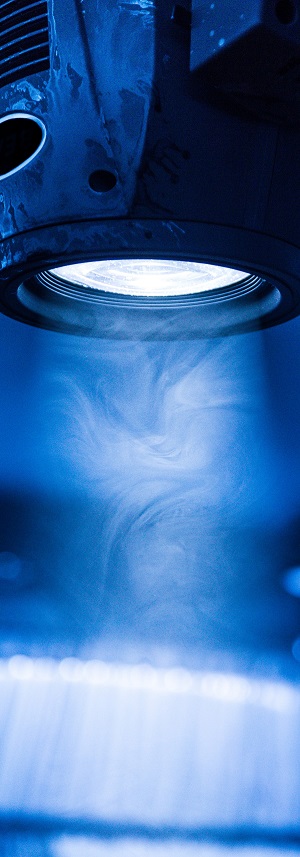
The purpose of this PhD project is to develop models to simulate the mechanical properties of PM and possibly also AM materials. This includes modelling of the different types of microstructures, both heterogeneous and homogenous, that are typical for these materials. It also means being able to take different levels of porosity into account, from the typical PM steel with around 5-10% porosity to AM materials with almost no pores.
The initial part of the project aims at characterization of the microstructure of the materials. This includes experimental determination of the mechanical properties of the different constituents but also the porosity. In the latter case both size and shape of the pores are of interest and the results should be compared with corresponding ones predicted by a numerical tool developed at the Department of Materials Science at KTH.
With the intial analysis completed, the second part of the project concerns micro- and macromechanical modelling of material at issue. In particular, finite element modelling will be attempted based on the information from the experiments discussed above. Different (static) loading situations will be investigated and the numerical results will be compared with corresponding experimental ones in order to determine the accuracy of the finite element procedure. The influence from the size and shape of the pores will be investigated.
The third part of the project will be mainly devoted to simulate, by using the finite element method, the static mechanical properties of the materials. Strength prediction is of great interest here and accordingly experimentally determined failure modes have to be included in the numerical modelling. Pertinent experiments have to be performed for this purpose (but as an alternative, could also be performed in the first part of the project).
The fourth and final part of the project is a continuation of the third part. However, here fatigue properties are at issue. It goes almost without saying then that the experiments above should be pertinent to both static and fatigue loading conditions.
The four parts described above defines the present Ph.D.-project which is funded by Höganäs AB. Part of the project time will be spent in Höganäs.
The personel involved in the project are as follows:
- Ph.D.-student at the Unit of Solid Mechanics, KTH: Vladilena Gaisina.
- Industrial supervisor at Höganäs AB: Michael Andersson.
- Ph.D. supervisors at the Unit of Solid Mechanics, KTH: Peter Gudmundson and Per-Lennart Larsson (main supervisor).
- Ph.D. supervisors at the Department of Materials Science and Engineering, KTH: Manon Bonvalet and Joakim Odqvist.